“Furch Guitars Sound Quite Distinctive and Special”: These Sublime Acoustics Deserve Your Serious Attention
Timeless in tone and style, yet built with advanced luthiery techniques – we travel to the Czech Republic to find out more
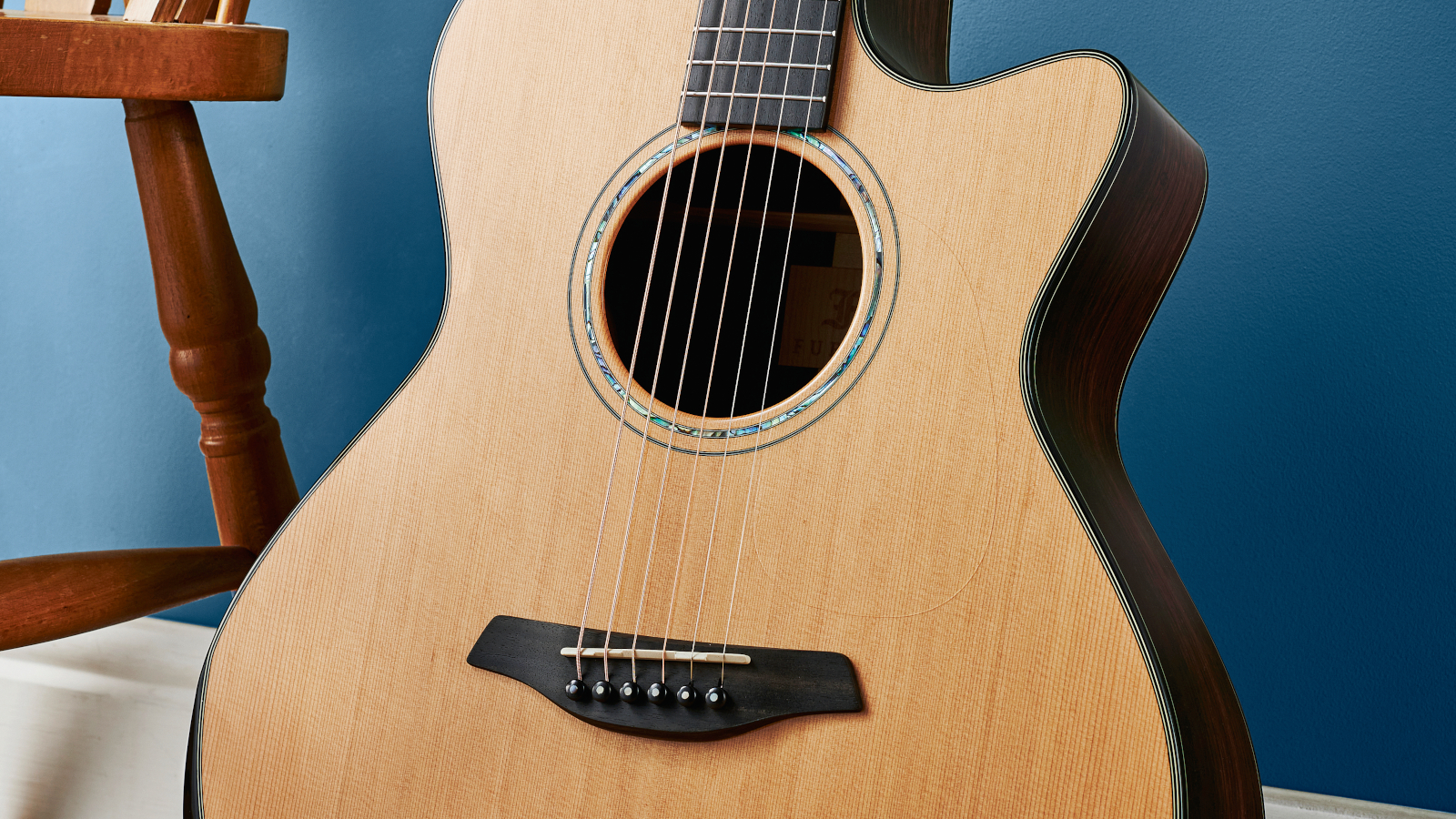
Most of us know that vintage acoustic guitars can be a little inconsistent in quality. We accept that some are diamonds, while others don’t shine quite so brightly. After all, isn’t that part of the mystique of things built the old-fashioned way?
The trouble with that theory is that, while everyone loves a nice, resonant old guitar, no one wants to own one of the bad ones. And that really summarizes what modern luthiers are trying to do through the union of handcraft and technology today: make better guitars, more consistently.
Few companies embody this approach as completely as Furch. In fact, the company, which is based in the Czech Republic, has revolution in its blood. Founder František Furch built his first guitar in 1981 because so few good acoustics were available.
“Back then, Czechoslovakia was under a tight communist regime,” he explains, “which didn’t allow us to travel almost anywhere, let alone to the countries of the Western Bloc. Quality instruments were available in Western European countries, but due to travel bans, these were not accessible to us at all. On top of that, even if one managed to get a permit to travel outside the country, most of us couldn’t afford to purchase them, due to the financial situation.”
Basic nylon-string guitars, made in the countries of the former Soviet Union, were available to Czech musicians, but, as an avid fan of U.S. bluegrass and country music (an underground activity at that time), František realized the only way he could obtain a good steel-string guitar was to build it himself.
He eventually did this using reclaimed wood from an old piano, which he paired with a fibreglass body inspired by Ovation acoustic guitars, which were becoming popular in the West at that time. Soon, musician friends from the underground bluegrass and country community started taking an interest in his guitars.
“I started keeping a list of all interested buyers, and I began spending my nights building custom guitars,” František recalls. “However, there was also a downside and a potential risk in all of this. As I said before, the totalitarian communist regime we lived in did not allow citizens to own private businesses, and it was absolutely forbidden to manufacture or grow anything for profit, under the threat of punishment, even long-term imprisonment. Luckily, a great relief came when the Velvet Revolution finally brought about liberalization and freedom.”
All the latest guitar news, interviews, lessons, reviews, deals and more, direct to your inbox!
After the fall of communism, Furch was finally able to open its doors as a legitimate business in 1990. František moved on pretty quickly from his early copies of Ovation guitars to original, all-wood designs. But because of his background in engineering, he developed his own unique approach to luthiery.
Petr Furch, František’s son, and the present-day CEO of Furch, explains. “My father has a great talent for understanding how different materials work – metals, different kinds of wood,” he says. “He has a good imagination for that. So he can invent really creative construction techniques for guitars. I can show you machines my father built 20 years ago that we still use today.”
The Hunt for Performance
Furch’s factory is located in the hamlet of Velké Němčice, near Brno. It stands at the edge of undulating farmland, and the building itself, made of weathered brick, was once a mill. It’s a far cry from the featureless industrial units in which many guitar firms are based. Inside, the old mill is alive with sound and activity, and the aromatic scent of seasoned tonewoods being sawn. Greeting us in the courtyard, Petr Furch leads us on a tour of the place.
Venturing onto the noisy factory floor, it’s apparent that combining traditional luthiery with bleeding-edge tech is absolutely core to how Furch makes guitars. A good example is Furch’s Composite Neck Reinforcement System, which Petr shows us ready to install on a partly built neck.
As many readers will know, a two-way truss rod is the standard mechanism for adjusting a guitar’s neck relief. Housed inside the neck, the truss rod exerts a varying degree of pressure on either end of the neck, depending on how an adjustment nut is set. This counteracts the natural tendency of the neck to bow forward under string tension.
Normally, a truss rod is a pretty simple device, made of metal. Furch, however, coaxes extra performance from its guitars by encasing its truss rods in carbon-fiber tubing before fitting them inside the neck. Why give the humble truss rod the Formula 1 treatment?
“The general problem with [a conventional truss rod] is that when you start to turn it, it pushes on the beginning and the end of the neck,” Petr explains. “But wood is a natural material and each piece behaves slightly differently, even if you dry it very carefully. So when you start to push [at either end of the neck], you will have very little control over what’s happening between these two points – and the wood is basically deciding what’s going to happen. So the neck can develop humps, it can twist and so on,” he explains.
“We figured out that if you put the truss rod inside a carbon pipe, it applies tension to the beginning and on the end of the neck, but now the pipe ‘decides’ what’s going to happen. Carbon is very rigid and the bending of carbon is very smooth, so it’s predictable, and, because it’s an artificial material, very homogeneous. So the neck then doesn’t have a tendency to twist or develop humps.” Petr adds that this carbon-reinforced design imparts extra strength and stability to the neck, which means that your preferred setup should stay just as you like it for longer.
Furch also unlocks extra performance from its guitars by using tools 20th century guitar makers didn’t have access to. This includes using advanced robotics to do certain jobs – the kind of precise but repetitive tasks that even well-motivated people eventually get bored of during a long day’s work, leading to lapses in quality. This is particularly important when sanding highly sensitive areas of the guitar, such as the soundboard, as inconsistencies here can hold back the instrument’s potential.
The factory’s humidity is also precisely controlled in critical areas, such as the room where bracing is fitted to soundboards. Again, the aim is for the finished guitar to be free of distortions or tensions in the wood that might impair the finished guitar’s tone.
Giving Wood a Voice
The most intriguing of Furch’s advanced luthiery techniques is voicing. Traditionally the preserve of boutique instruments, the soundboards of all Furch guitars, including its entry-level Violet guitars, are individually voiced to deliver the best possible sound.
The team at Furch are a little secretive about the exact process they use, but, in essence, they analyze each soundboard to determine its raw acoustic properties, then precisely adjust the thickness of the top to enhance desirable sonic attributes. On Furch’s top-of-the-line Red and Rainbow series guitars, both the top and the back are individually voiced.
“We’re very proud of voicing,” Petr says. “We started to do the first version of the voicing process in 2008. Back then it was a very simple thing – we could actually measure some physical properties of the soundboard, and we could basically adjust the thickness of the whole soundboard based on what we found. Today, we still measure those physical properties, but we adjust the thickness of various areas of the top, and by that we have much better control over the acoustic output of the soundboard.”
If that all sounds a bit dry and scientific, the results are anything but, leading to excellent sonority and clarity in the “voiced” instruments we’ve tried. But despite the evident value of high-precision tech, human handcrafting skills are still centrally important to Furch, Petr explains, using the example of binding. “It actually comes down to what are the abilities of humans and what are abilities of some sort of machinery,” he reflects.
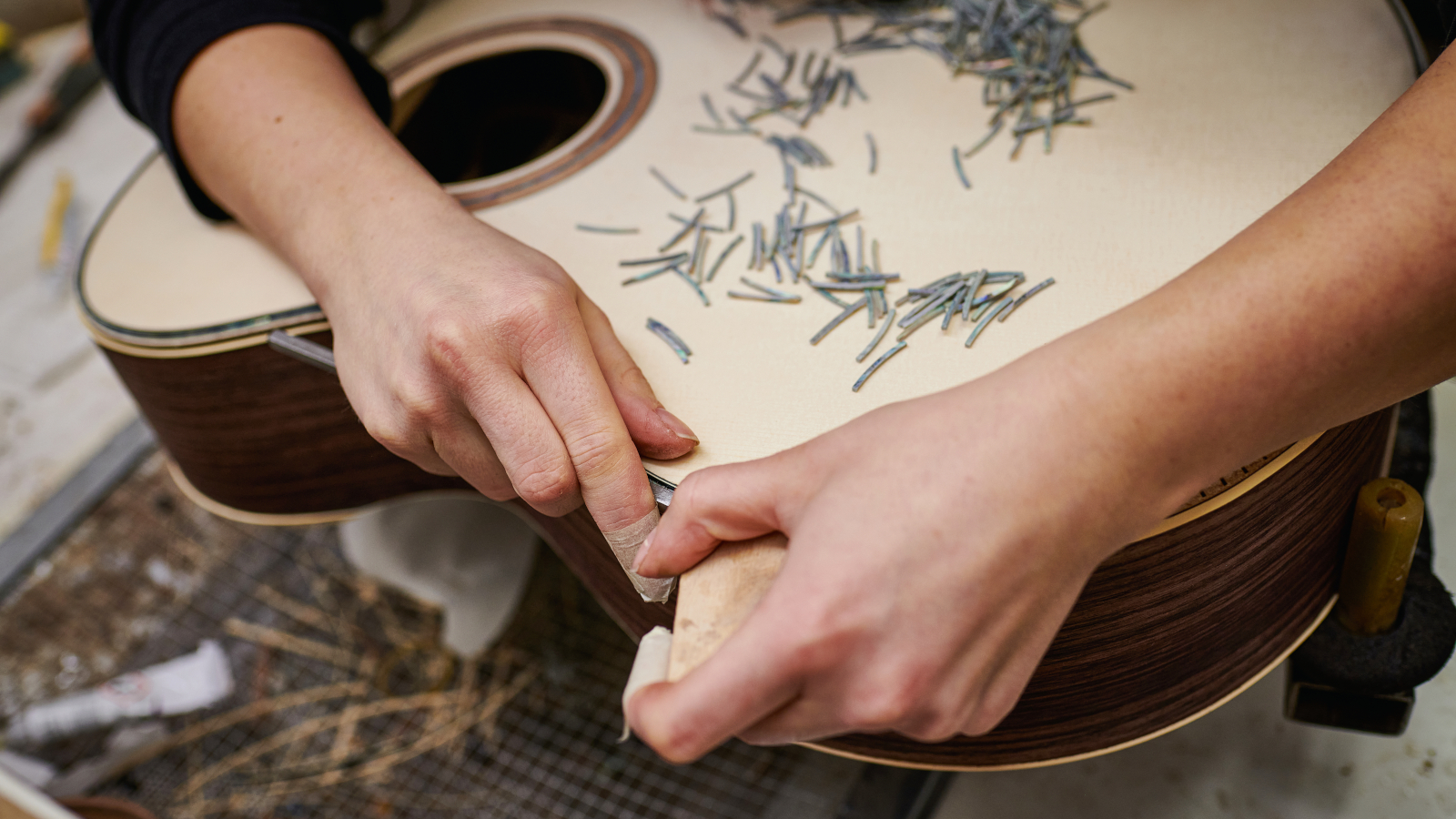
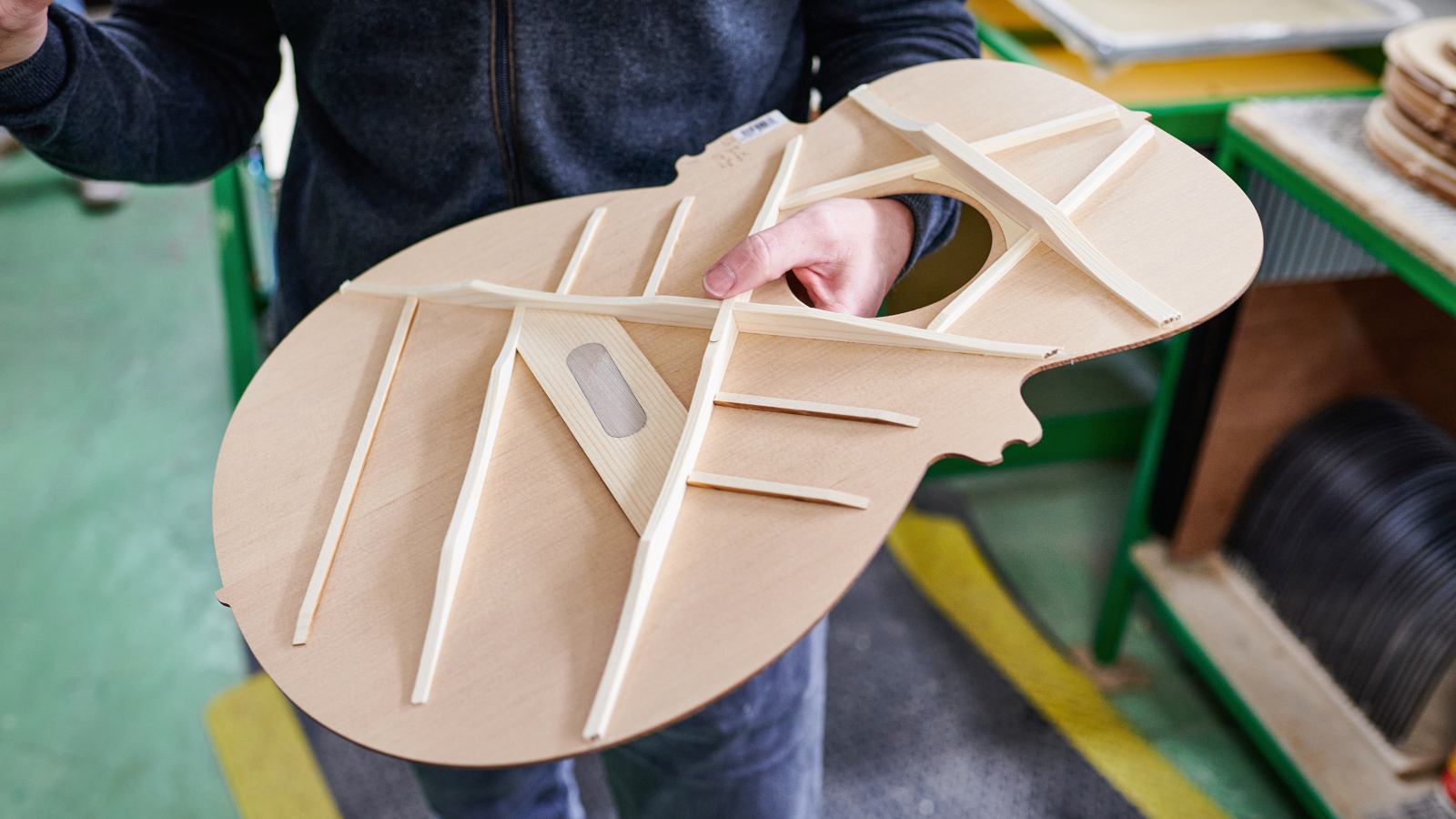
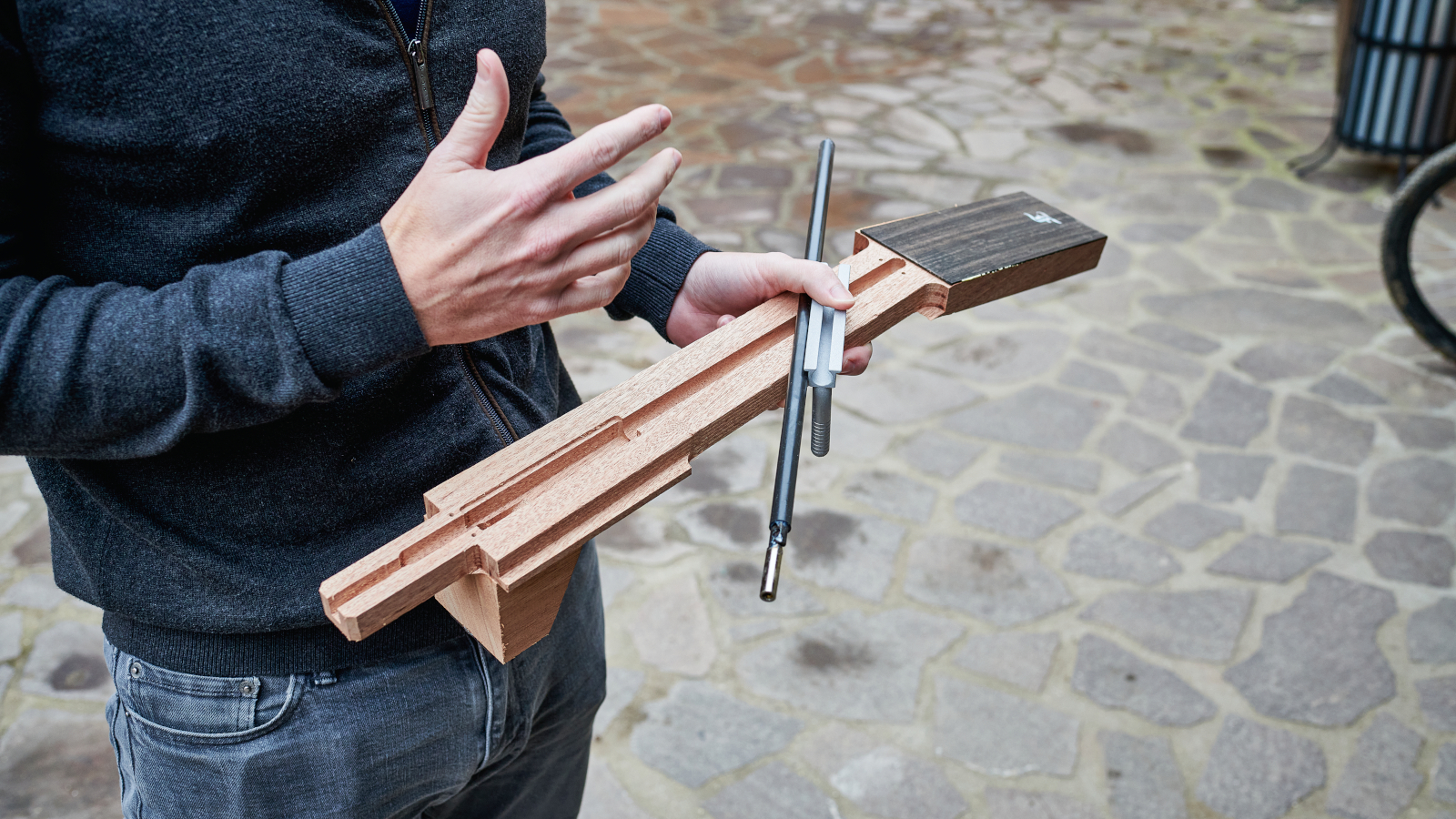
“We humans have a very cool skill and it’s decision making. In order to get high-quality binding, you have to make thousands of micro-decisions, and that’s human territory; we are very good at that. But we are maybe not so precise in doing the same thing 100 times because we get bored, we get tired, we get distracted. But decision making is really a thing we do really well.”
Walking through the factory with the company’s namesakes, we’re left with a sense of being inside the manufacturing equivalent of an orchestra, in which Petr and František are the conductors. “We’re looking into sustain, tonal-spectrum balance over the whole fingerboard, overall volume of the guitar and dynamic spectrum of the guitar,” Petr says. “Those are things we try to measure and improve, individually or all together.
If your creation is helping to bring joy to other people, it’s the ultimate contribution to society
Petr Furch
“This is the scientific approach, but then there is a part that is more intuitive, which is really only that we – my father and I – basically imagine or have the vision for the sound Furch guitars should have. I think that’s also why Furch guitars sound quite distinctive and special.”
Earlier that afternoon, we’d enjoyed watching an excellent Czech guitarist named Rudy Horvát put a variety of Furch guitars through their paces in different tunings. We asked Petr how he feels when he sees his creations being played to the full.
His answer explained why the instinct to improve the things we care about can be so powerful. “What better is there?” Petr replies. “If the audience and the musicians like it, and I can see that our guitar is part of that, then what’s better? If your creation is helping to bring joy to other people, it’s the ultimate contribution to society you can make as a human being.”
Why are Furch guitars grouped by color?
Furch’s product line groups guitars by color. The Violet series, which starts from about $1,280, represents the entry level, and the ranges go up through Blue, Green, Yellow, Orange and Red series, with the Rainbow grade (from about $3,530) as Furch’s Custom Shop offering.
Furch’s designs are typically offered with either Western red cedar tops, which Petr Furch believes have a natural compression that aids fingerstyle performance, or Sitka spruce for clear articulation and energetic dynamics.
Furch offers a variety of woods, from padauk to rosewood, for the back and sides, and dreadnought, OM and Grand Auditorium body styles are available, as are specialist models like the Little Jane travel guitar.
How is Furch pronounced?
While it’s usual to rhyme Furch with “church,” the correct Czech pronunciation is closer to “Foork.”
Visit Furch Guitars for more information.