Players
Latest Players
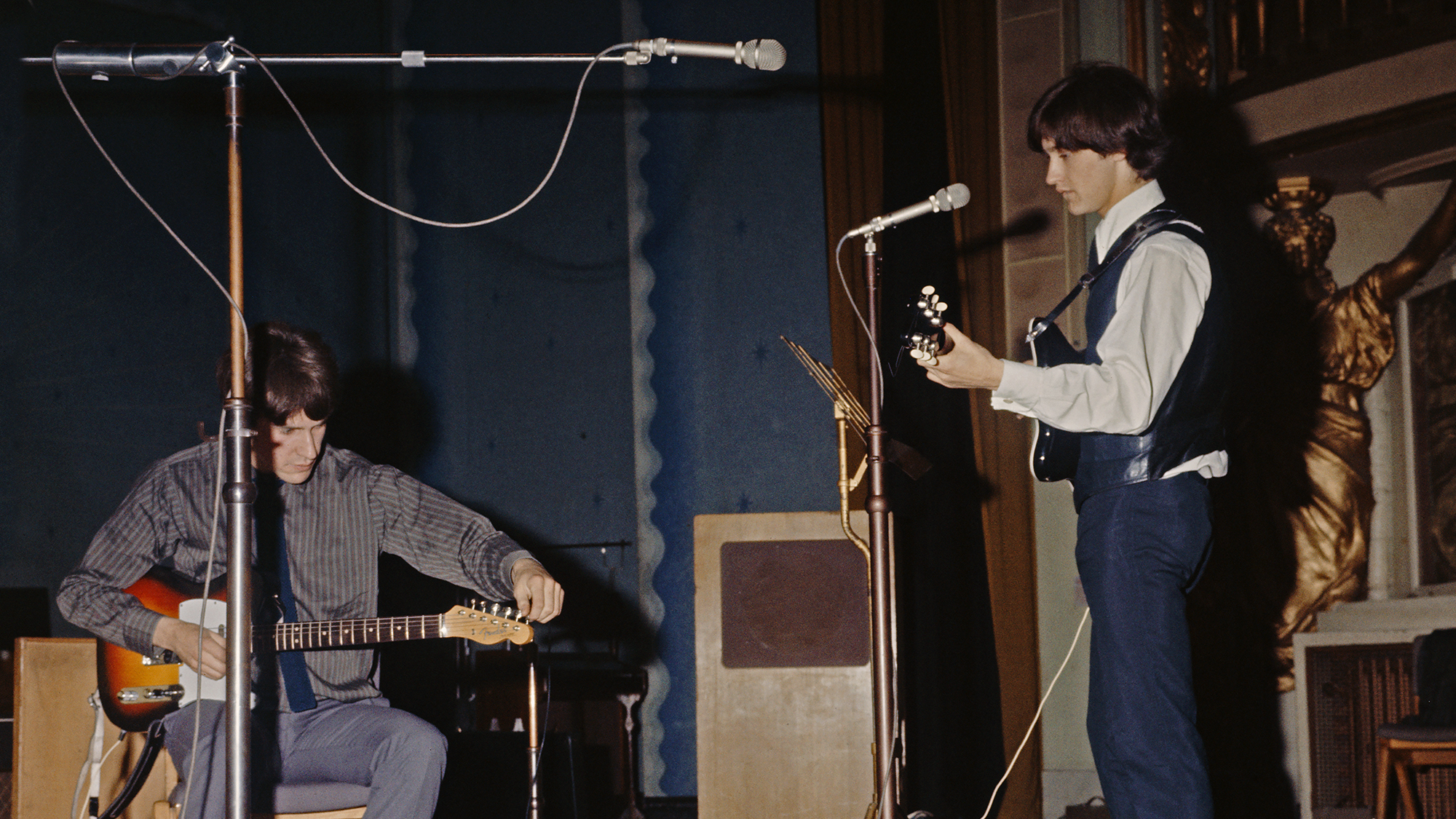
Dave Davies on the speaker-slashing skills that turned on Pete Townshend, Jimmy Page and Jeff Beck
By Elizabeth Swann published
The guitarist blamed boring guitar sounds and his own love of imperfection for his actions, saying, "That sound was born out of total frustration"
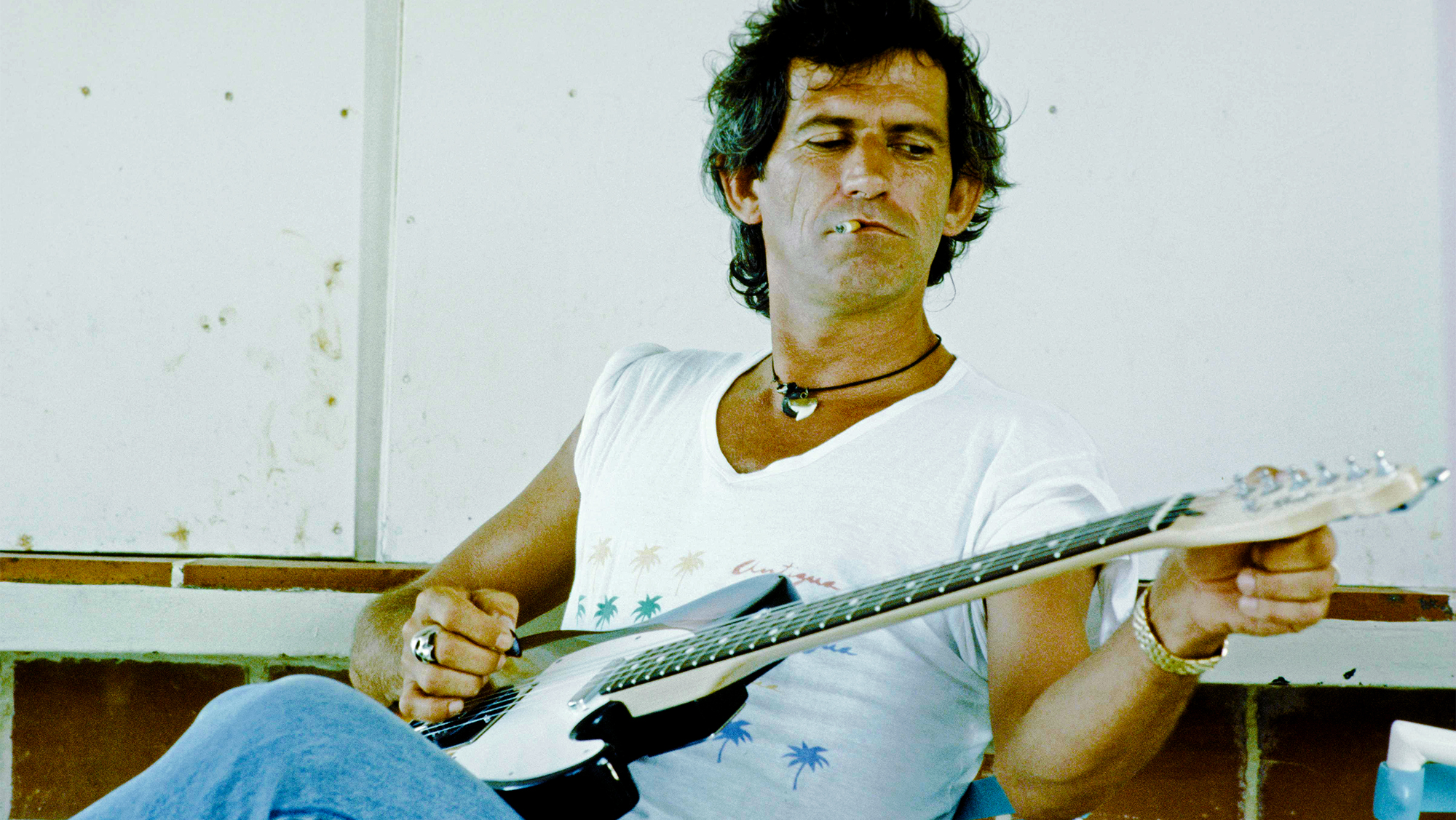
Brian Jones, Mick Taylor or Ronnie Wood? Keith Richards says one guitarist was the wrong fit
By Christopher Scapelliti published
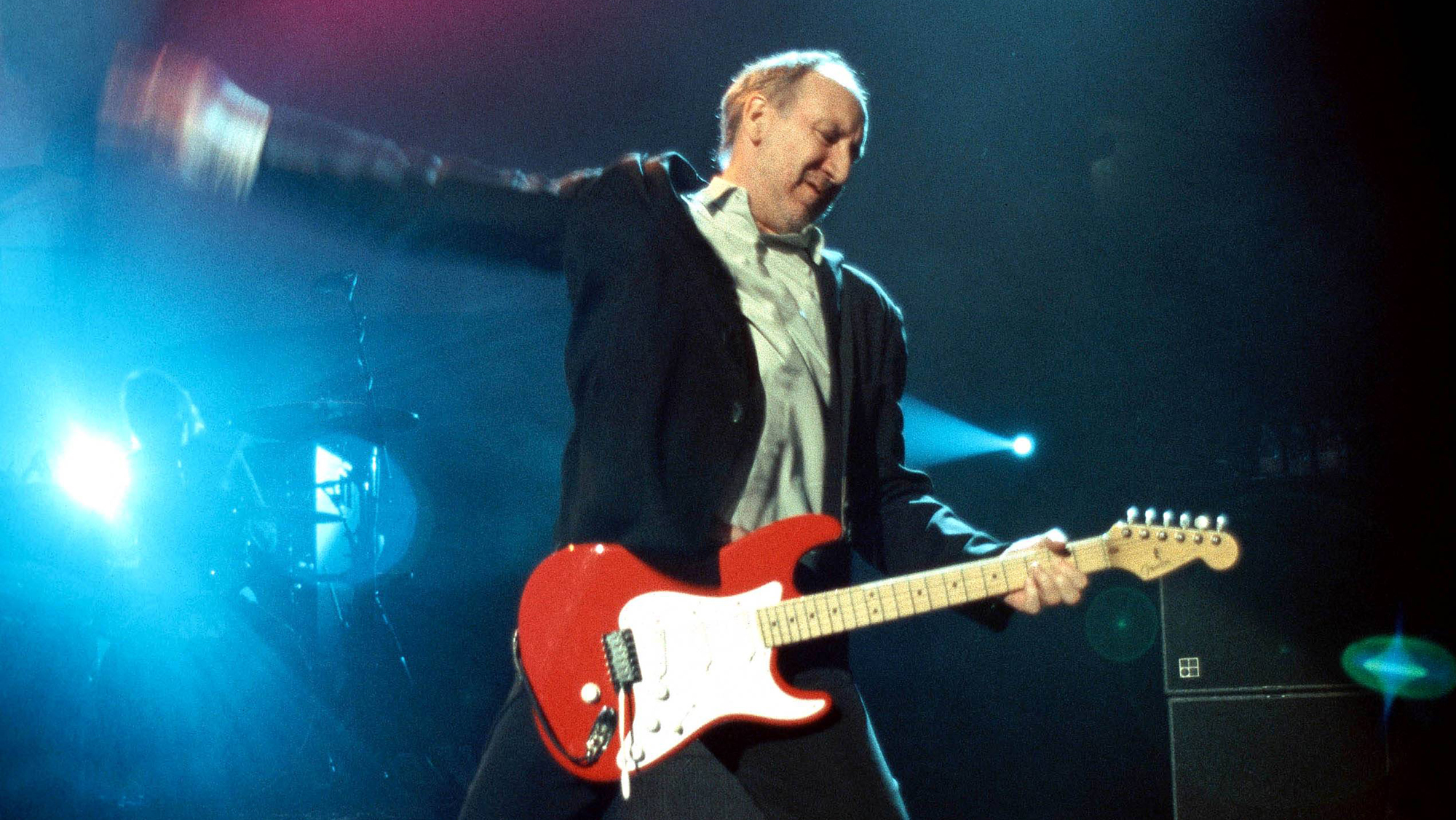
Pete Townshend explains the correct way to do the windmill guitar strum
By Christopher Scapelliti last updated
As the guitarist explains, the windmill is fraught with danger, including fingernail tears and hand lacerations
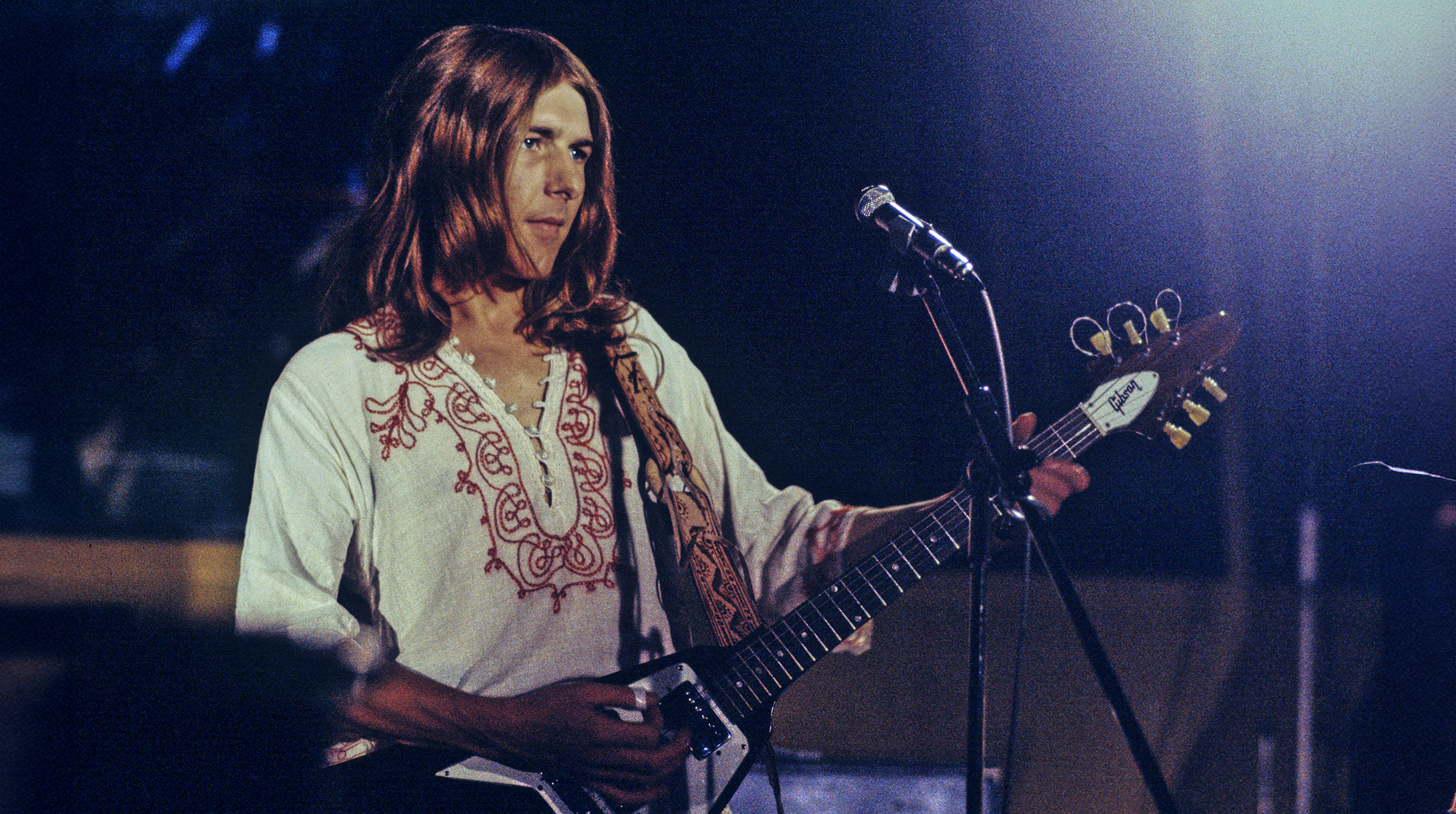
Mick Ralphs on the influence of Leslie West and the glorious guitars that rocked Mott the Hoople and Bad Company
By Jas Obrecht published
In our 1979 interview, the guitarist told us about his key axes — from his first "misfortune" to the Les Paul Standards that graced his collection in the 1970s
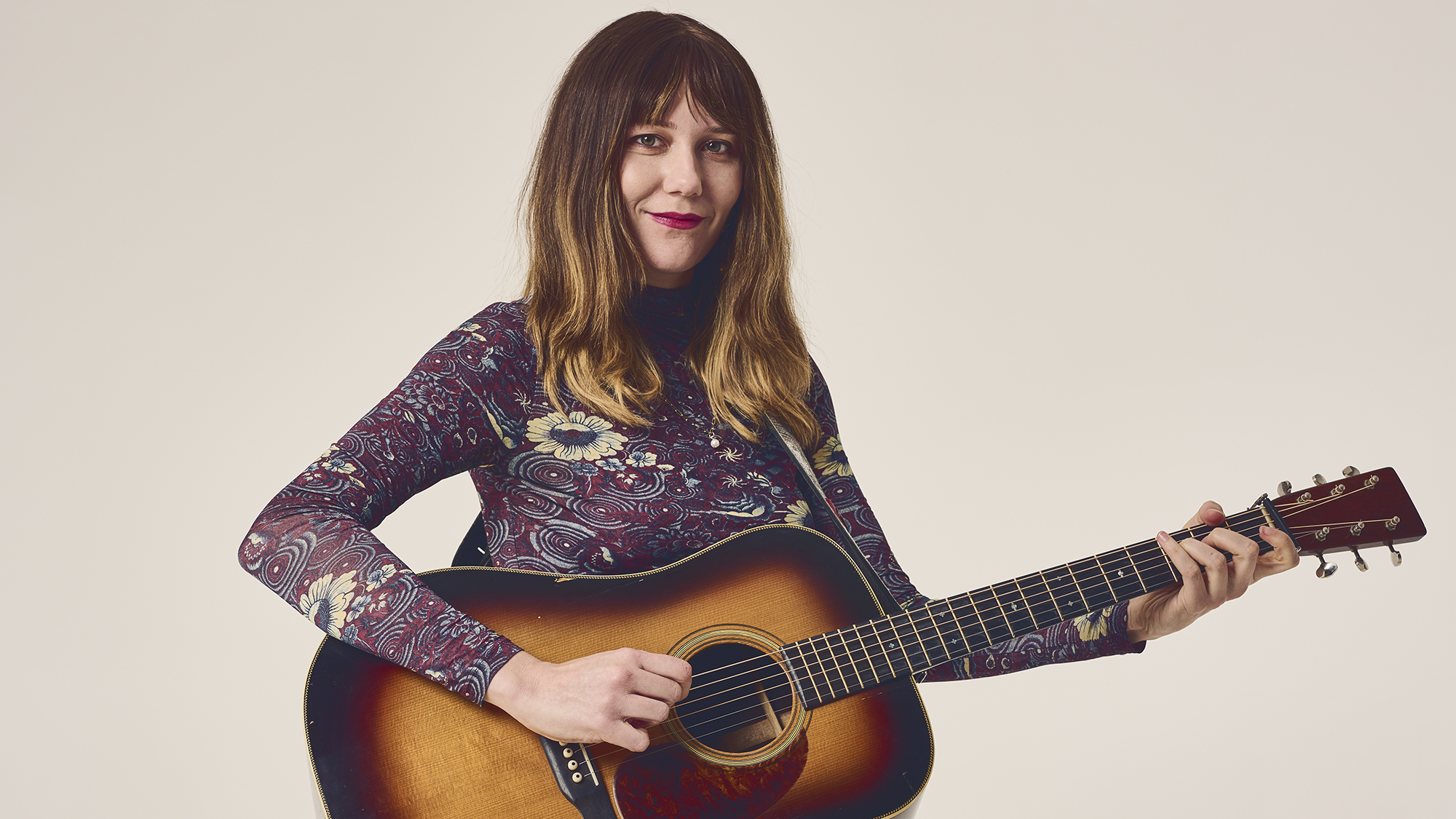
Molly Tuttle on what makes all the difference when it comes to choosing a guitar pick
By Elizabeth Swann published
Now 21 years into her career, she reveals a surprising choice when it comes to the plectrum that works best for her style of bluegrass flatpicking
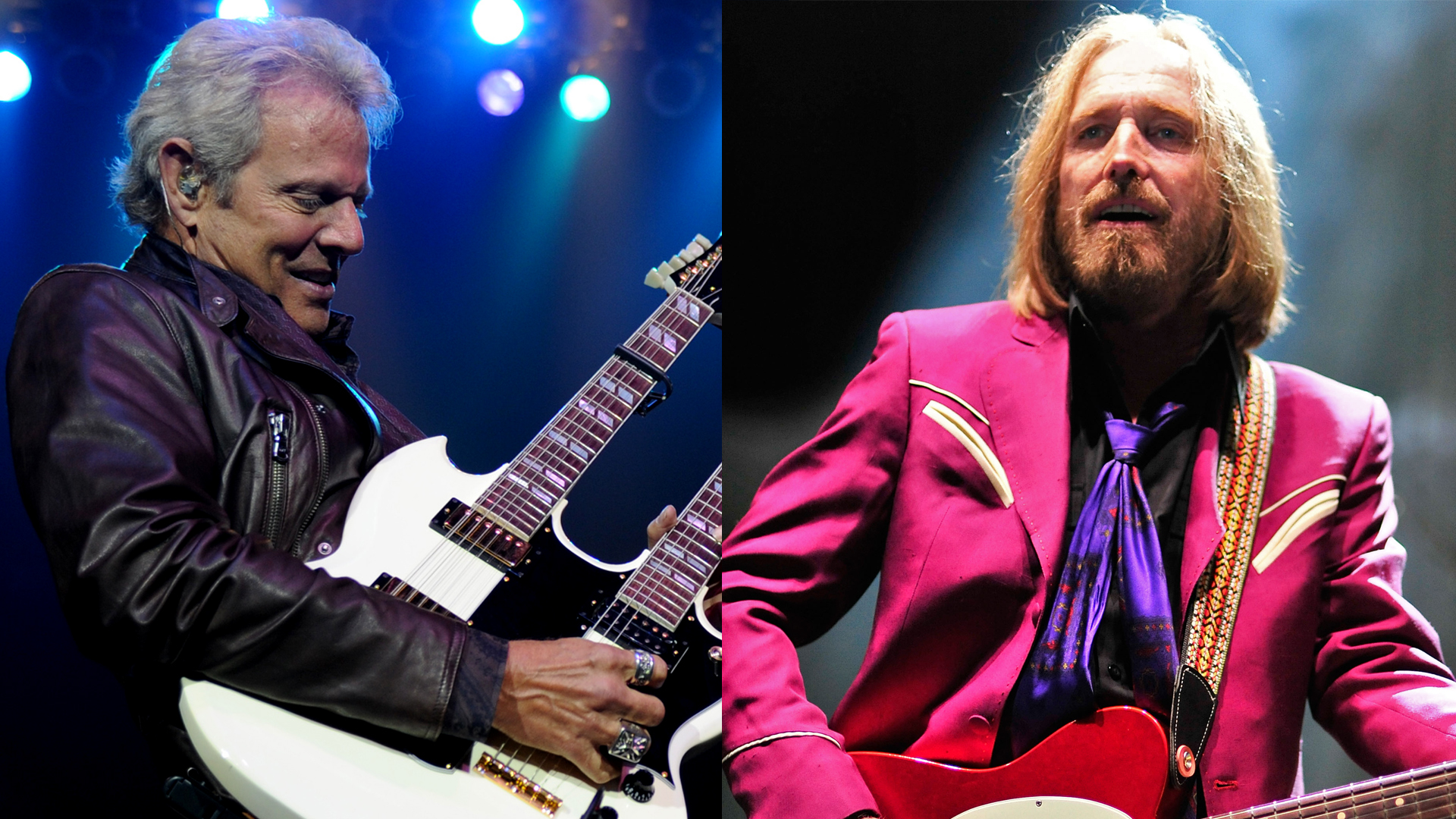
Don Felder on his early years with Petty, Stephen Stills, Duane Allman and Florida's burgeoning rock scene
By Christopher Scapelliti published
“I can’t tell it was something that was in the water or something in what we were smoking," the former Eagles guitarist remarked of Northern Central Florida's impact on rock
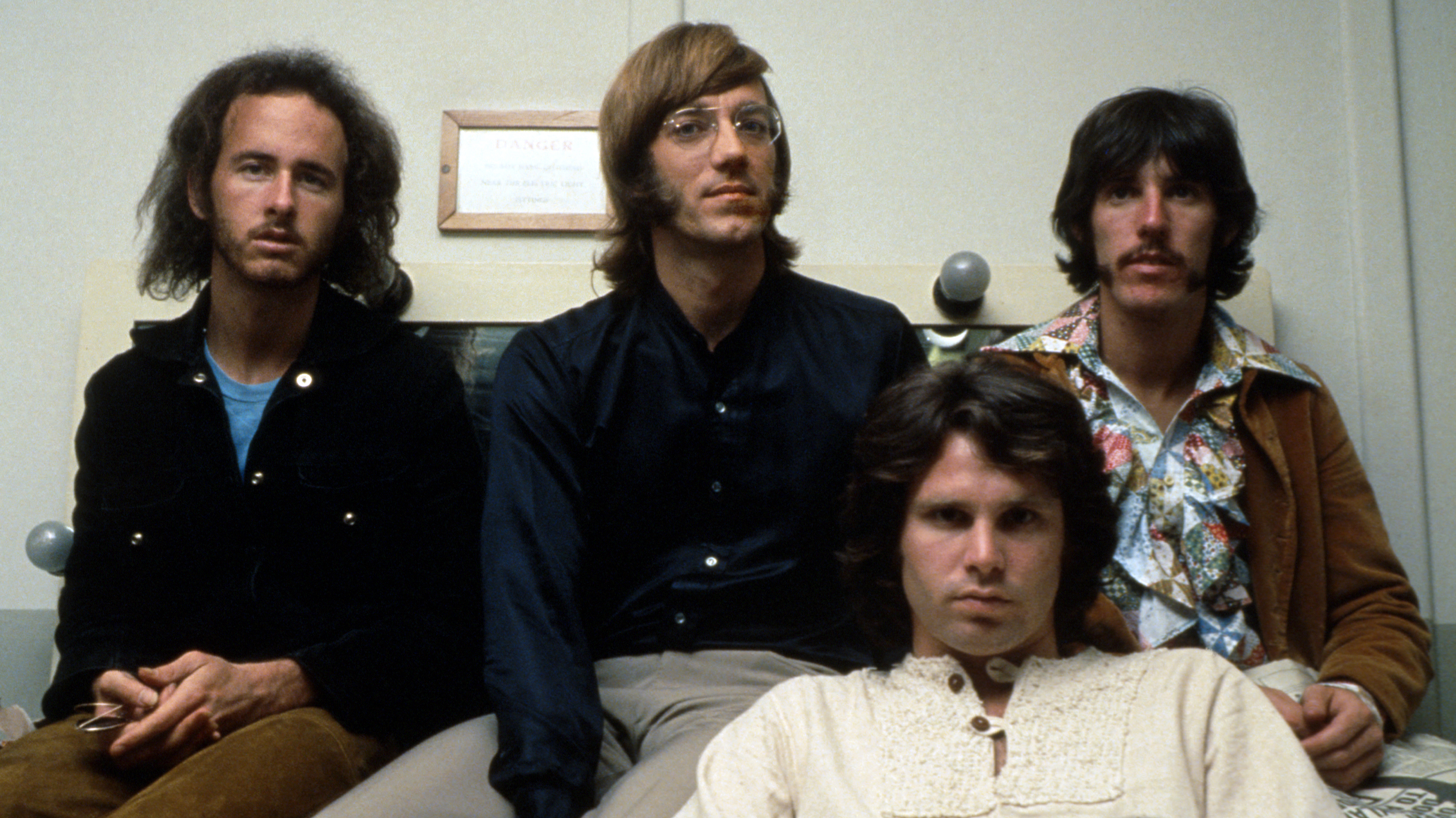
Robby Krieger on the Doors’ "stupid" decision to carry on without Jim Morrison
By Phil Weller last updated
Contractual obligations forced the three remaining band members to release three more albums before calling it a day
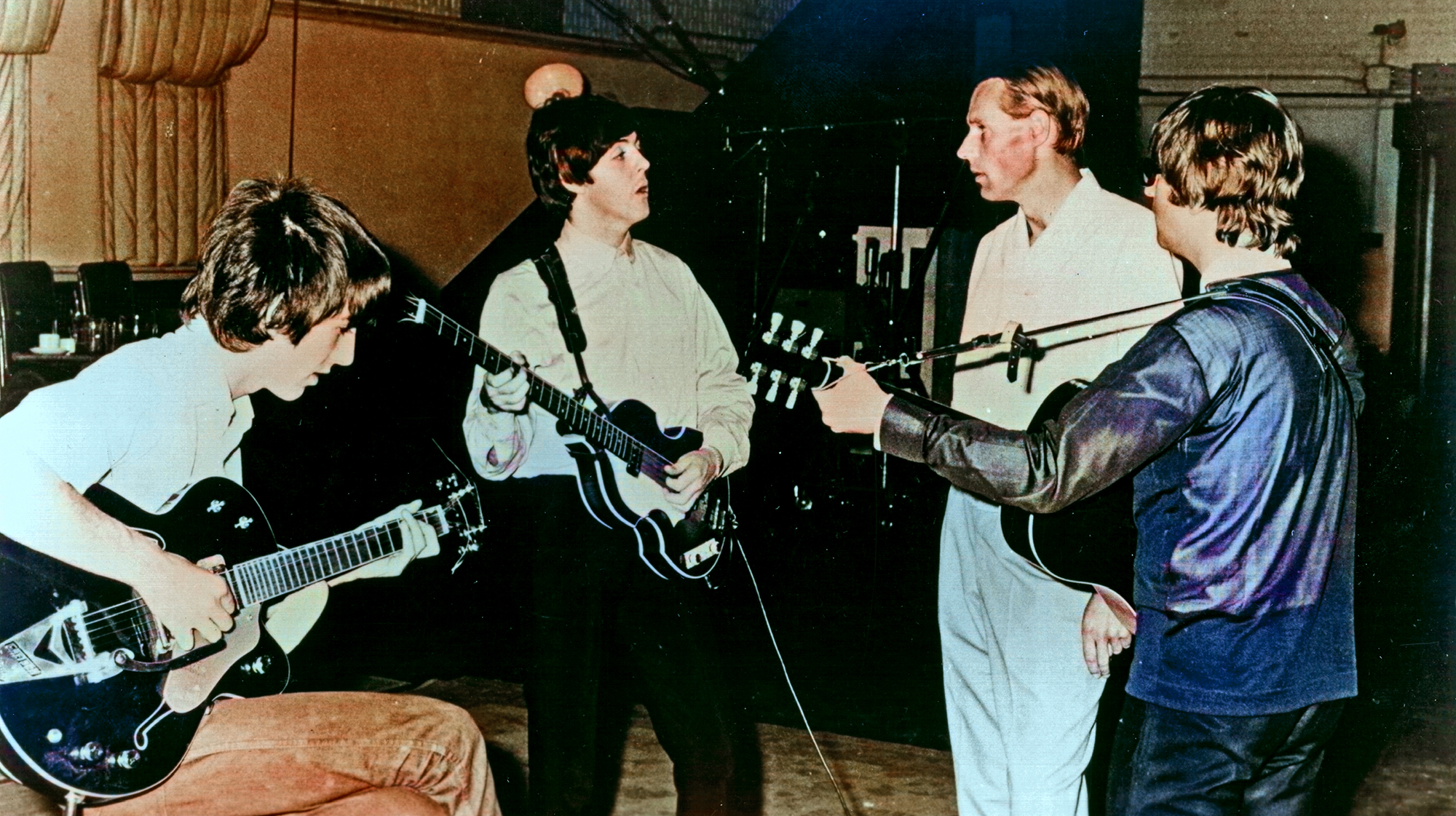
Paul McCartney reveals three Beatles techniques that explain why they stood out from every other rock and roll band
By Christopher Scapelliti published
From performance to recording and arranging, McCartney said the group found ways to make themselves a little different from the competition
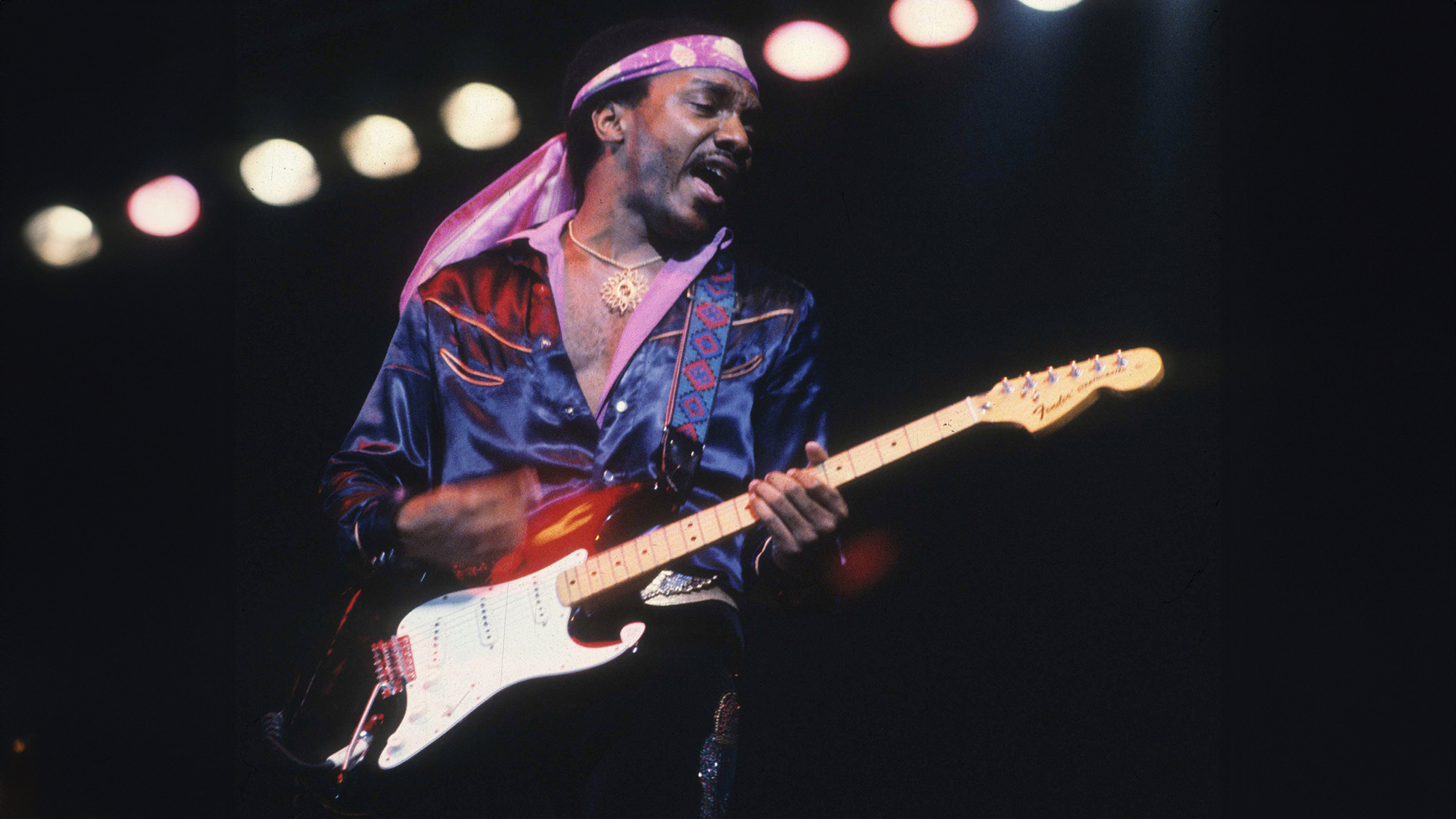
Ernie Isley reveals the sonic ingredients behind his iconic fuzz guitar tone on the Isley Brothers hit “That Lady”
By Andrew Daly published
The guitarist said he was forced to redo his solo when his first take left no room for the vocals. But it all worked out fine in the end
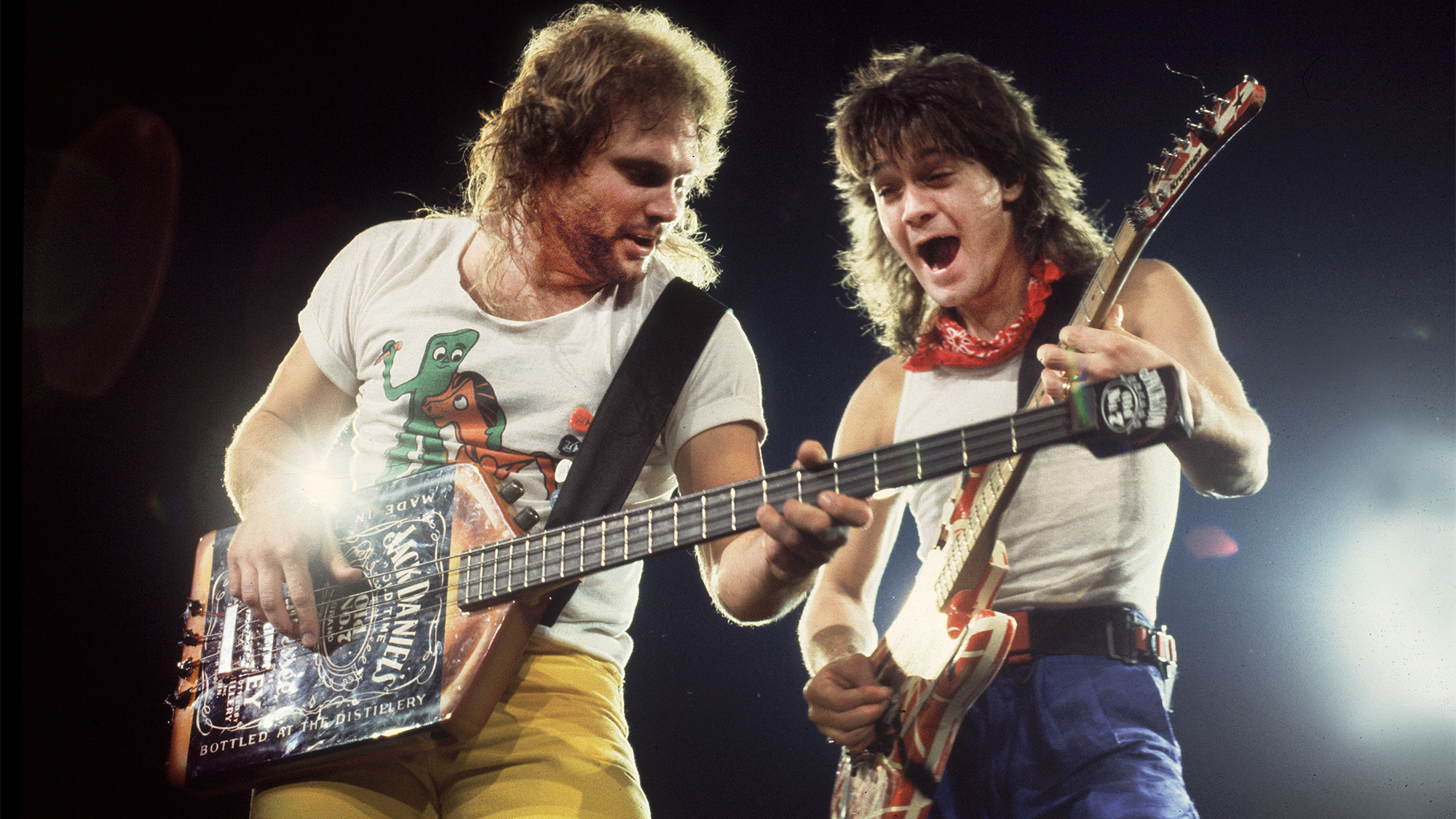
Michael Anthony reveals David Lee Roth's career-saving advice to Eddie Van Halen during Van Halen's early days
By Christopher Scapelliti published
The former Van Halen bassist says the singer was concerned other guitarists would steal Eddie's technique before the guitarist could establish himself
All the latest guitar news, interviews, lessons, reviews, deals and more, direct to your inbox!